The sun is shining in Hamburg, and the mild autumn air is in motion – even though I am perfectly equipped for rainy weather. In early October, shipbuilders from around the world gather in a conference hotel near the harbor for the CADMATIC Digital Wave Forum. The user meeting invites participants to experience CADMATIC’s CAD application for shipbuilding firsthand and to learn about current trends, product innovations, and new developments. The highlight: CADMATIC Wave, an integrated CAD/PLM solution specifically designed for shipbuilding and jointly developed by CADMATIC and CONTACT.
Model visualization simplifies data retrieval and collaboration
After our first coffee, we slowly make our way into the conference hall. The morning is filled with numbers and facts around CADMATIC’s digitalization strategy. In the afternoon, our Managing Director Maximilian Zachries presents CADMATIC Wave to the 200 participants. As we demonstrate the first functionalities of the integrated Product Data Management (PDM), some attendees quickly pull out their phones to snap a photo of the feature. I am somewhat excited – now it’s official. Now we also need the data model. And that isn’t quite so simple.
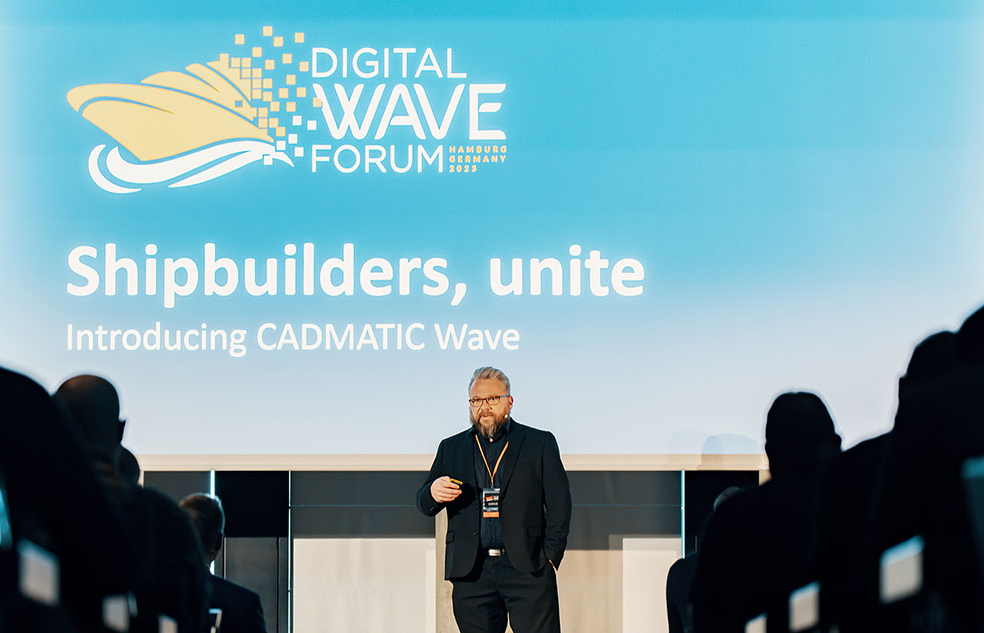
CADMATIC’s Atte Peltola presents CADMATIC Wave. (© CADMATIC)
The resounding call for a data model for shipbuilding carries me through the three days in Hamburg. During my conversations with industry colleagues, it becomes evident that the information required and generated in the shipbuilding process must be able to be mapped within the model. Model-centric is the magic word: the ship’s geometry is visualized, including equipment, fittings, and logistics. Information can then be retrieved and added via the specific parts of the model. Model visualizations provide a shared and intuitive view of the ship for all involved trades, significantly simplifying information retrieval. This enhances the efficiency of engineering activities and collaboration, also with partners.
Basing a data model on ship geometry is challenging
Engaged in a discussion with a research associate from the Norwegian University of Science and Technology (NTNU), we stumble upon a question: Is the geometry model even suitable for generating a generic product structure for data storage in the PDM? After all, as a placeholder in a data model, there are quite a few locations in such a ship. And let me put it this way: data models are typically organized along the processes in product creation, not the geometry of a ship model. I am curious to see how we will solve this challenge in CADMATIC Wave.
The evening event takes place on the Cap San Diego, a museum ship in the Hamburg harbor. The rustic flair of a ship’s belly and the lavish buffet create a cozy atmosphere for lively conversations. We talk about life in Finland and Norway and the difference between information and data management. The evening ends stormy and rainy, and I finally put my rain gear to good use and return to the hotel dry and warm.
SEUS brings European shipbuilding to a new efficiency level
At the CADMATIC Digital Wave Forum, I also meet my consortium partners from the Smart European Shipbuilding (SEUS) project for the first time. Among them are representatives from NTNU and CADMATIC, as well as employees from two shipyards, the Norwegian Ulstein Group and the Spanish Astilleros Gondan SA. SEUS is an EU-funded research project with the goal of developing an integrated CAD and PLM solution for shipbuilding. This endeavor goes way beyond the functionalities we develop in CADMATIC Wave. For instance, we aim to incorporate knowledge management and utilize AI for searching within product data.
In this context, the broad positioning of our research department, CONTACT Research, works to our advantage. Our focus areas include not only Digital Lifecycle Management, where we conduct research on digitalization strategies for various industries, but also Artificial Intelligence. The AI product data search we aim to implement in SEUS allows us to bring our self-declared motto to life: “Bringing artificial intelligence into the engineering domains.”
As three days in Hamburg come to an end, three strong impressions remain:
- It is necessary to design an abstract data model for shipbuilding. One that contains the modules of a ship and yet can be customized to fit the specific needs of any shipbuilder. This data model must be closely linked to the development process.
- Personal exchange and meeting each other face to face have been an enriching experience for me in this new work area. This positive feeling motivates me for my future work in the SEUS project.
- In Hamburg, rain gear is a must.