“Personas are just start-up knick-knacks, and for business software just a gimmick!” I’m sure many product developers have heard this before. I certainly have. But what is the truth behind the criticism that personas offer relevant added value for consumer products and are just creative add-ons for business software?
What are personas anyway?
Personas are fictitious people who represent typical representatives of a specific target group. They give product developers, customers and stakeholders an idea of who uses the product. In addition to a photo and name, personas typically include information on age, profession, free-time activities, family status and curriculum vitae, as well as typical needs and fears.
Personas in the context of business software
However, how do I deal with this as a product developer when my target group is primarily not people with individual needs and ideas, but with concrete professional challenges? For example, whether digital asset manager Diana Asmussen likes to play computers in her free time or go on vacation with her dogs is of no interest to product development. Diana steps into the spotlight with her professional needs as a digital asset manager and her requirements for an IoT system. When designing business software, employees should be addressed who want to complete their tasks efficiently and act in their roles and company processes.
CONTACT’s Personas
We at CONTACT therefore decided to create personas based on their roles and associated tasks within a fictitious company. We obtained input from our internal subject matter experts and customer interviews. Each persona has a task description and information on how to use CONTACT Elements.
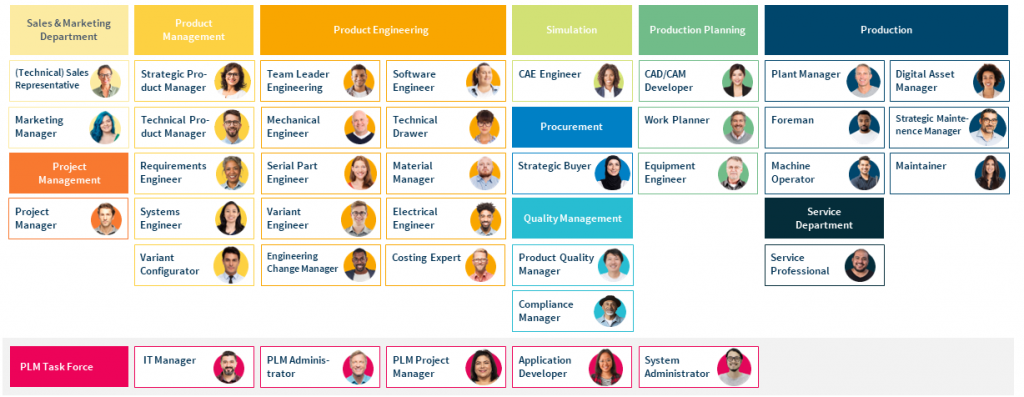
To be more specific, this means…
The holistic view of user needs provides valuable added value for product development – from knowledge building to quality assurance.
Personas make users more tangible and help new and long-standing product developers to get to know our target groups better.
By answering questions like: Who works with the 3D Cockpit? What does a user do in variant management? Or with whom does a CAE engineer interact? they know exactly for whom they are developing and can serve requirements in a more targeted manner. As sample users in concepts, demos and review systems, including all the rights they would have in a real environment, personas also ensure that work during development and quality assurance is user-centric.
But personas also have a high added value outside of product development. In presentations and in consulting, we use them to vividly depict scenarios, to build up understanding, and for identification.
So my answer to the initial question of whether personas are a gimmick or offer sustainable added value is clear: Personas are a central element in developing the best possible software for the user. They clarify needs, help to prioritize requirements, and promote a sustainable build-up of knowledge about the target groups company-wide.