When someone asks me something about Material Data Management, I always counter by asking what exactly is meant by “material”. This may not be the answer the other person expects at that moment, but it saves us both long minutes of confusion and talking past each other. The reason: not all materials are the same.
About the ambiguity of language
As a Frenchman in Germany, I am used to the fact that ambiguity leads to misunderstandings. Some expressions cannot be translated one-to-one from one language to another – at least not in such a way that it is immediately clear to everyone what is meant. A well-known example is the word “Gemütlichkeit”. The term only exists in German. More insidious, however, are the so-called false friends: word pairs such as “gift” in English and “Gift” in German. They look the same, but the meaning is fundamentally different. Even as an experienced polyglot, one is not protected from this. For example, my French interlocutors may seem irritated when I say that something has “irrité” me, meaning that something has surprised me. However, they understand this to mean that I have got some kind of skin rash out of sheer annoyance.
What can lead to funny and even sometimes slightly embarrassing situations in everyday life often causes inefficiency in the working world. To find examples, we don’t even have to look in an international context: Even within a German-speaking organization, not everyone necessarily speaks the same language. This is not due to the strong dialects in many places, but to the disciplinary nature of the language: Different people with different qualifications or expertise can understand different things by the same word.
And that brings me to the topic of this article. More precisely, to the multilingual mesh and the interdisciplinary ambiguity of the word “material”, whose galactic confusion around the terminology I would like to resolve.
Material is not equal to material
Enterprise software is a lot about managing materials and their data. There are great solutions for this. They are called Materials Management or Materials Data Management or even Master Material Data Management. The names sound very similar and are often used synonymously in practice. Yet they refer to completely different things. Freely following the motto “material is equal to material”, it is overlooked that the word can have a different meaning for different disciplines and things are lumped together that have little to do with each other. Confusion and misunderstanding are guaranteed.
Differences within the disciplines
In production logistics or material requirements planning, a material is a logistical unit, a resource that is needed for some value-adding process. Goods that can be purchased, such as a screw, a flange, a spindle, a tire, and so on. The art of sensibly procuring, moving and storing materials is called “Materialwirtschaft” in German and Materials Management in English.
In the context of product development, materials in this sense do not play a role. Development is not interested in the hood and where it is stored, but only in its description. To put it in the language of information technology: Development defines classes, production logistics manages instances of these classes. However, the concept of material reappears here as well, because in linguistic usage, items, parts, and assemblies are readily called materials. The reason for this is that they become materials in the sense of production logistics at the interface between PLM and ERP. This gives rise to misleading terms such as Material Management or Material Data Management. It would be more correct to speak of Master Data Management in the sense of parts master management.
In engineering (including design and simulation), the word material describes the physical composition of an object in the sense of materials science or materials technology: i.e., whether an object is made of wood, PA66, Inconel, or GFRP, for example. This is obvious. The management of all information about materials and their properties is called Material Data Management. Confusingly, the acronym MDM also stands for Master Data Management, which is not particularly conducive to sharpening the terms.
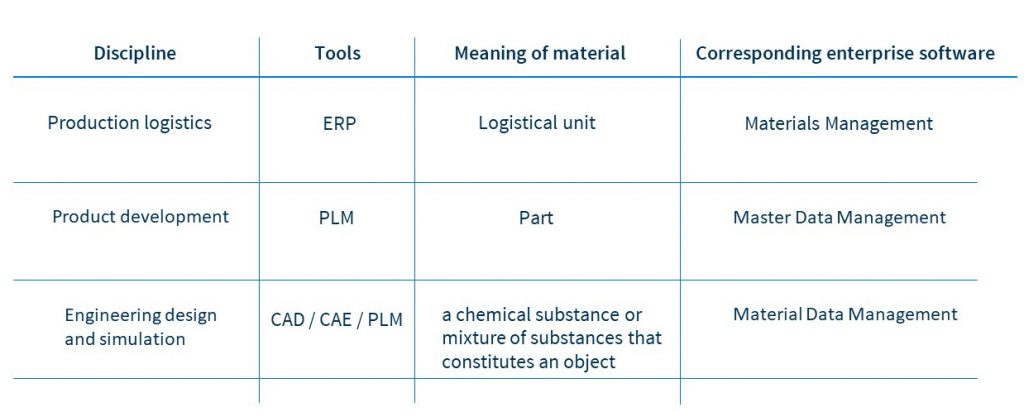
Conclusion
The confusion is great. PLM solutions that are tailored to the respective disciplines provide a remedy. They serve the different requirements optimally and thus ensure better collaboration overall. With Master Data Management as a core PDM function, all parts master data can be kept consistent and managed efficiently. Modern Material Data Management stores all information on materials and serves as a reference for the entire product development process. Material Compliance helps document the quality-checked delivery of regulated materials and precursors and ensures that only approved substances are processed. With interfaces to ERP systems, digital materials (in the sense of development) then also easily make the step into the physical world and become materials in the sense of production logistics.