Künstliche Intelligenz (KI) ist in aller Munde und spielt auch in der Produktentwicklung eine immer größere Rolle. Doch wie lässt sich diese Technologie sinnvoll in Entwicklungsprojekte integrieren? Gemeinsam mit unserem Kunden Audi haben wir die Probe aufs Exempel gemacht und die Potenziale und Herausforderungen einer Machine Learning (ML)-Anwendung – als Teilbereich von KI – an einem realen Projekt untersucht. Für den Einsatz wählten wir ein Crash-Management-System (CMS). Es ist einerseits einfach genug, um ein nutzbringendes Ergebnis zu erreichen und gleichzeitig kompliziert genug, um die generelle Anwendbarkeit der der ML-Methode hinreichend zu testen.
Fachwissen als Schlüssel
ML lässt sich nur insoweit sinnvoll nutzen, wie es die zugrundeliegende Datenbasis erlaubt. Deshalb spielt das Know-how der beteiligten Fachleute eine entscheidende Rolle. Zum Beispiel geben Konstrukteurinnen und Konstrukteure ihr Wissen über Fertigungs- und Bauraumbeschränkungen, verwendbare Materialien und Abhängigkeiten in das CAD-Modell. Berechnungsingenieure und -ingenieurinnen teilen ihr Wissen über den Simulationsprozess und die Data Scientists unterstützen beim Sampling und der Auswertung.
Die Erstellung tausender Design- und korrespondierender Simulationsmodelle, wie sie für den Einsatz von Machine Learning (ML) erforderlich ist, stellt ohne Automatisierung eine enorme Herausforderung dar. Die FCM CAT.CAE-Bridge, ein speziell entwickeltes Plug-In für CATIA, ermöglicht eine nahtlose Automatisierung über alle Prozessschritte hinweg. Darüber hinaus verankert sie alle Informationen für die Simulation (Material, Eigenschaften, Solver und viele weitere) bereits im CAD-Modell. Die vollautomatische Übersetzung in ein Simulationsfile erfolgt dann mit Tools wie ANSA oder Hypermesh.
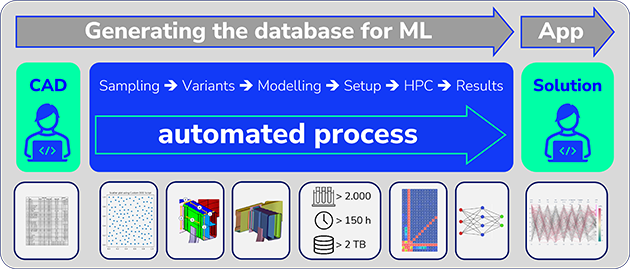
Präzise Verknüpfung von Parametern und Ergebnissen
Unser Ansatz gewährleistet, dass die Beziehung zwischen dem CAD-Modell und dem Simulationsmodell vollständig erhalten bleibt. Die automatisierte Berechnung und Auswertung der Modelle auf die spezifischen Ergebnisse hin schafft eine sehr gute Datengrundlage für den ML-Prozess. Die Vektoren aus Eingabeparametern mit korrespondierenden Ergebniswerten stellen die Basis für den ML-Ansatz – eindeutig und umfassend.
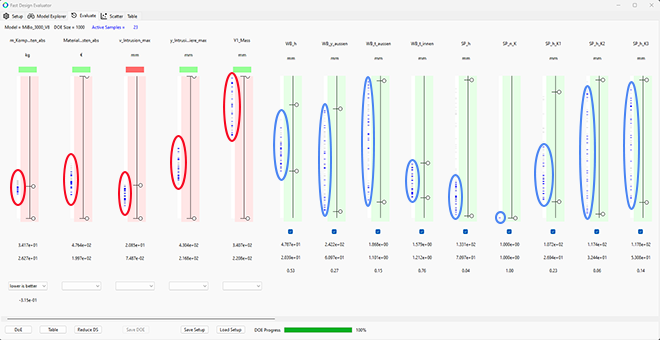
Auf den damit trainierten Modellen und der darin bekannten Genauigkeit lassen sich dann schnell Parametervariationen durchspielen und die Auswirkung auf das Verhalten ableiten, buchstäblich in Minuten. Sobald die optimalen Parameter identifiziert sind, werden diese automatisch in das CAD-Modell übertragen und der Designprozess kann fortgesetzt werden.
Fazit
Unser Projekt hat gezeigt, dass ML eine valide Methode für das Design-Engineering ist. Die Kombination aus parametrischen CAD-Modellen, Simulation und Machine Learning bietet eine effiziente Herangehensweise, um Designentscheidungen schnell und präzise zu treffen. Voraussetzung dafür liegen in einer robusten Datenbasis und in der Zusammenarbeit der relevanten Know-how-Träger am Modell. Die guten Ergebnisse aus dem Audi-Projekt zeigen das Potenzial unseres datenbasierten Ansatzes für die Produktentwicklung.